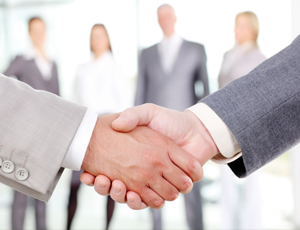
Setting the “Standard of Excellence” for Quality, Service and Price, by which all companies in the Brass Rod Industry will be measured.
Adinath Started as a small family run unit, and has since grown into one of India’s leading Brass Rod Extruders. At our state of the art hydraulic extrusion plant in Jamnagar- India, we produce bars in round, hex, squares, rectangles, hollows and made to order shapes for customer specific applications. In addition to Brass Rods, our product line comprises of various grades of Copper Alloy Ingots and a wide range of Brass Components catering to the need of the customers.
At Adinath, we develop our product lines with a concerted effort to meet the broad spectrum of needs demanded by customers throughout the Indian Sub-continent and abroad.
Our Plant utilizes induction heating, Billets/Ingots casting, billet heating, direct extrusion, straightening, material handling and modern process control equipment. Standards of quality are maintained continuously throughout each process, from validation of raw material to the final semi-manufactured product, using our state of the art optical emission spectrometry (OES) laboratory; fitted with a patented UV PLUS chamber utilizing arc and spark excitation technology.
Over the years our customers have come to appreciate our commitment to quality, innovative solutions and careful pricing and we welcome any inquiries you may have and look forward to the opportunity to work with you to make your application of brass rods, bars, ingots and components a success.
Manufacturing Process
AEPL begins the manufacturing process with best quality imported brass scrap mixed with virgin metals to ensure flexibility in meeting changing customer requirements. Cast Billets are subjected to test with optical emission Spectrometer to certify exact chemistry required by the customer. Extrusion of these casted billets produces defect free material in the shapes of round, hex , squares, flats and hollow forms in pre-defined lengths. The extruded material is then pickled to prepare the surface for cold-drawing. Finishing die reduces the cross section to obtain precise tolerances. Surface finishing, straightening, machinability, physical and mechanical properties are improved through the process to meet specific customer requirements.
AEPL is fully equipped with Grinding, Drilling, and Threading, Automatic and Semi-Automatic machines and CNC machines along with testing equipments such as calipers, all standard gauges with “GO” and “NOT GO” threads, gauges, micrometers, electronic verniers and profile projectors which ensures us to manufacture the components as per specific tolerance and quality. Over the years we have developed a wide variety of products, samples of which are available upon request.